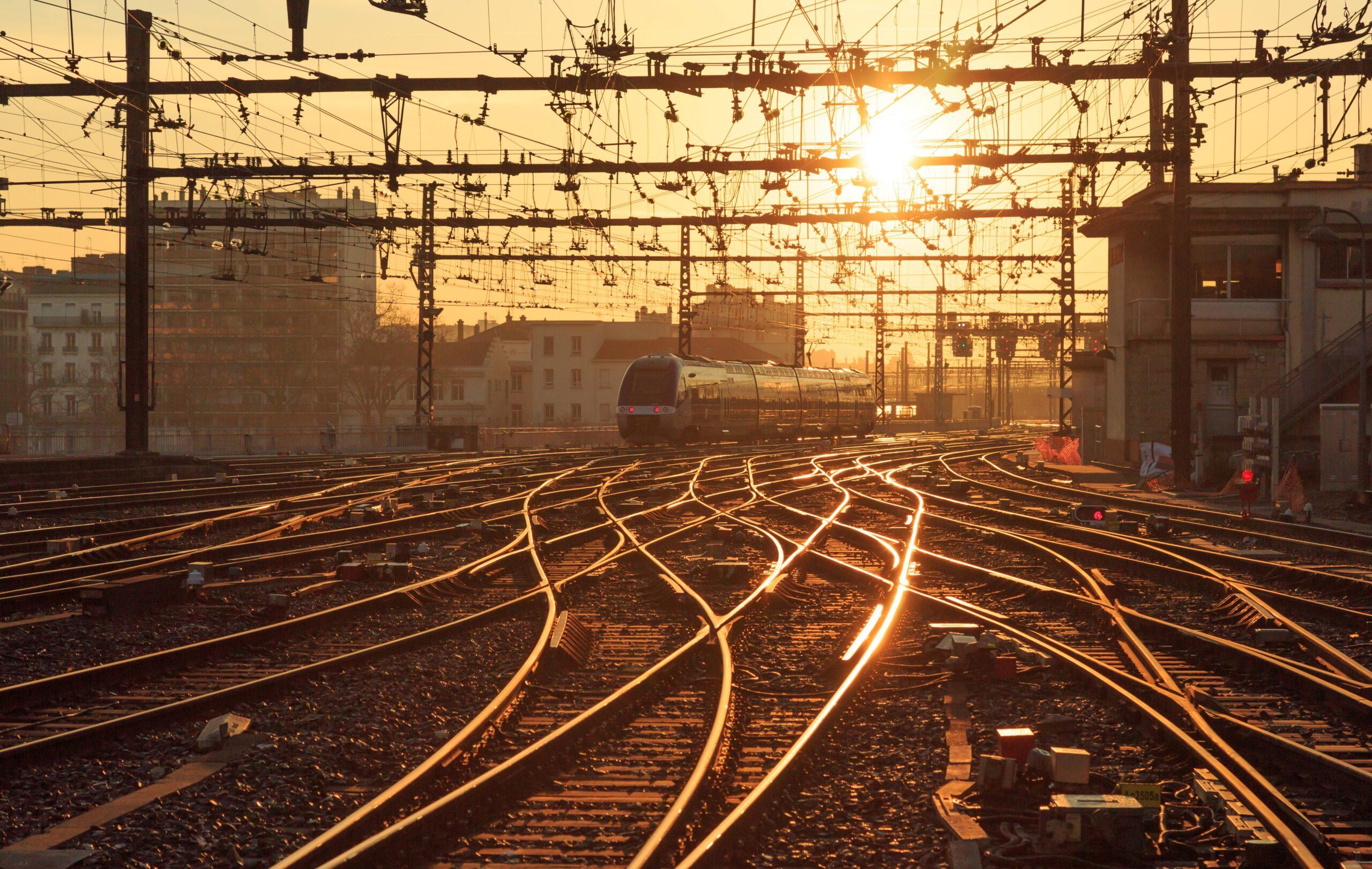
Adobe Stock 138718634
AI Tool Would Enable Industry to Predict Temperatures that Require Maintenance or Repair, Improving Safety and Making Repairs Less Expensive
Continuously welded rails were a cost game-changer in the railway industry, which contributes over $27 billion to the U.S. economy. But a continuous rail can’t expand and contract with temperature like short segments of rail with a small air gap between them. A team from the University of Pittsburgh used PSC’s flagship Bridges-2 supercomputer to simulate how the expansion and contraction of rail segments affects sound moving through them. They used these data to train an artificial intelligence (AI) algorithm to predict when a given stretch of rail will generate dangerous buckling or breakage.
WHY IT’S IMPORTANT
As addicted as we are to our cars and trucks in the U.S., our economy couldn’t work without rail transportation. Trains can carry heavier loads for longer distances than trucks, at lower energy costs. In 2020 the railway industry directly contributed $27.7 billion in economic output, generating nearly 240,000 jobs, with even more in indirect and induced contributions.
Having said that, there is one way in which rails are more expensive than roads. Building and maintaining a rail system, as well as the staffing needed to do so, is pricey. These costs came down considerably in the late 1960s, when the world’s railways started incorporating continuously welded rails. These rails are quicker and cheaper to lay down than tracks involving short lengths of rail that butt up against each other, with a small air gap between them.
With the cost savings of continuously welded rails came downsides, though. Steel rails expand and contract with the temperature. Unlike air-gapped short segments of rail, a single rail stretching for as long as multiple miles can expand in the heat enough to buckle, or contract in the cold enough to snap, called “pull-apart” in the industry. Either problem can cause a catastrophic derailment when a train goes over it. At best, they involve slowing or halting traffic. Replacing rails to avoid such risks, as well as lawsuits and revenue loss, costs the industry an average of about $10 million a year. Costs of catastrophic derailments, such as the one in East Palestine, Ohio, can be much higher, into the billions.
“You can think of a rail as an element … that is fixed at two ends. When the temperature goes high, it tends to expand, and because it cannot expand, it generates compressive forces — and the opposite, of course, in winter, when there are traction forces. [During these] temperature extremes, there is either a buckling phenomenon … or rail fracture. The idea of the project is to predict the temperature at which these dramatic phenomena would occur. And we are tackling this prediction with a machine learning perspective, and machine learning needs a lot of data.”
— Piervincenzo Rizzo, University of Pittsburgh
The industry has methods to monitor and test rail segments to make sure they are intact and aren’t expanding or contracting too much. But these methods involve closing down that section of railway and cutting out samples of the metal, requiring repairs afterward. That’s why Matthew Belding, a graduate student working in the lab of Piervincenzo Rizzo, a professor of civil & environmental engineering at Pitt, wanted to develop an AI that could predict the neutral temperature of a given rail, allowing operators to determine whether the rail is susceptible to a significant amount of stress with changes in temperature. Their tool of choice for the work was PSC’s NSF-funded Bridges-2. They acquired time on the system through the NSF ACCESS program, in which PSC is a leading member.
HOW PSC HELPED
The proposed AI algorithm would monitor the status of rail segments by how sound moves through them. A given rail vibrates at a specific natural frequency. Picture a wine glass shattering when a singer hits a specific note. Stress impacts these frequencies; the Pitt team wanted to use this phenomenon to determine the stress in the rail.
Such a simulation would be simple to run on a conventional computer. But before it can be used, such machine learning needs a lot more data and computing power to train itself. The computer initially guesses at solutions to the problem, first using data where the “right answers” are labeled. When a guess is wrong, the labels help the computer adjust itself so that it pares back wrong predictions until it matches what the labeled data show. Then, it can be tested against unlabeled data to confirm its accuracy before being used on real problems.
The amount of data needed for the process couldn’t be gotten just from the relatively small number of expensive real-world measurements. Instead, Belding built a finite element model that simulated the known behavior of the steel and how sound moves through it. Such a model required a lot more computing power than available on a standard computer.
“Labeled data in the rail industry is not easy to obtain. So that’s the usefulness of the finite element [model]. But that makes it also difficult for us to generate a significant number of cases, unless we have that computing power. I know that some of the last simulations we did [on Bridges-2] were a little over 1,500 cases or simulations for specific resistances and specific temperature changes. That took right around two weeks … We estimated it for our computing resources, at least in the lab. It would have taken well over a year, a year and a half.”
— Matthew Belding, University of Pittsburgh
Bridges-2 filled this need by offering multiple powerful computing nodes. These enabled the team to simulate over 1,500 specific cases involving different types of rail in different temperatures, building up a dataset that allowed their AI to generate predictions as to how the rails would behave. The Pitt scientists then took their AI tool to the MxV Rail Facility in Colorado, where they could test its conclusions in a real-world railway designed for such research. The AI produced accurate predictions there, giving the investigators confidence they’re on the right track — pun intended — for real-life application.
The Pitt team is now working on expanding their dataset, with a goal of simulating another 4,000 to 4,500 cases. Another aim will be to simulate and accurately predict behavior in real-world railways that aren’t as uniformly constructed as the ones at the MxV facility.
The scientists have two separate eventual goals. One is a wayside detector, a stationary detector that monitors the effects on the rails as trains pass by. The current AI is capable of achieving this. The other goal is an in-motion detector. This would be attached to a vehicle and would allow quick data acquisition at multiple sites — very useful, given the extensive mileage that Class 1 railroads manage. These setups will complement the eventual optimization of the model towards unknown rail resistances, which is currently the largest unknown.