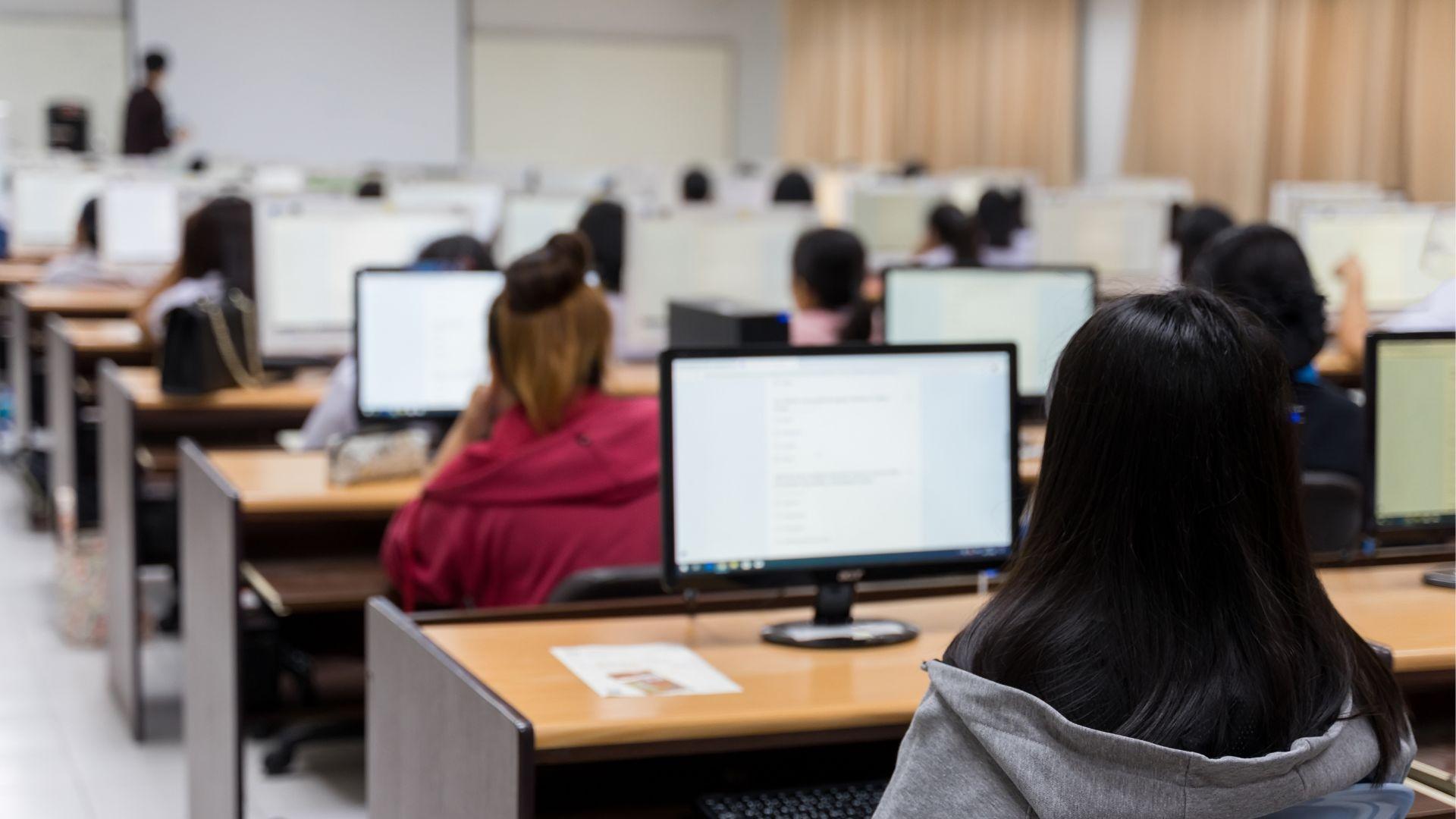
Resulting database will enable AI exploration of movement-sensitive electrical components
Piezoelectric materials — materials whose electrical behaviors change as they experience strain — promise breakthroughs in wearable electronics that monitor our health and recharge our devices as we move. But scientists don’t know as much as they’d like about these new materials’ behavior. Professors at North Carolina Central University (NCCU) helped their students use PSC’s Bridges-2 system to simulate the behavior of carbon nanotubes as they stretch and break. Their students collected the first data in what will become a vast database to help engineers discover, via artificial intelligence (AI), materials with desired properties for a given electronic device.
WHY IT’S IMPORTANT
Materials whose electrical behavior changes when they’re put under physical stress — called piezoelectric materials — have lots of possible game-changing applications. They can be used to create smartphone screens that respond to your touch even when you’re wearing thick gloves. (Current screens require your finger to conduct a tiny amount of electricity.) They can be incorporated into clothing that monitors your heart rate, breathing and movements, communicating with your smartphone and warning your doctor if you have a problem. They can even use your footfalls to collect energy that recharges your electronics as you walk.
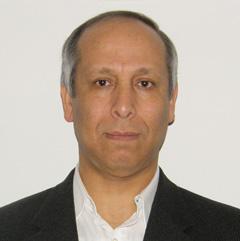
When they were discovered, [carbon nanotubes] promised a lot of new useful applications. Scientists were so excited about the possibilities that were going to be presented to materials engineers and industry. However, carbon nanotubes appeared to be more complicated than we thought in the beginning.”—Abdennaceur Karoui, NCCU
Most piezoelectric materials are ceramics, which are good for some applications but pose problems when a device needs to be flexible or not brittle. By blending polymers with newly discovered electrically conducting materials, such as nanorods or carbon nanotubes (CNTs) — microscopic tubes made of a cage of carbon atoms—materials scientists hope to create artificial piezoresistive composites with more flexibility and durability.
While piezoelectric materials are on the verge of expanding what we can do with personal electronics, progress in exploring these materials is much slower than scientists would like. Part of the problem is that the kind of computer-driven investigation that they’d like to conduct is being held back by a lack of data on these materials and details about their behavior. Constructing databases is a time-consuming, expensive, expert-human-effort-hungry job. That means slow progress.
Abdennaceur Karoui, Fozia Sahtout and Gaolin Zheng, scientists at NCCU, wondered whether they could harness the raw power of simulation on a supercomputer and the sharp minds of their students to tackle the database problem in a way that taught the latter how to excel at computational science. Their classroom offering would allow the students explore the properties of these amazing materials while learning how to employ advanced computers to crack scientific problems.
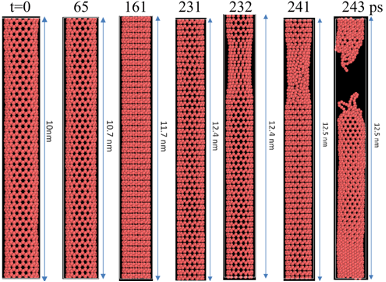
Snapshots from the molecular dynamics tensile test of one of the CNTs tested by the NCCU team. The applied force is vertical in the image.
HOW PSC HELPED
Scientists would like to use a type of AI called machine learning (ML) to explore the possible behavior of piezoelectric materials. In ML, the computer teaches itself by trial and error to predict properties of a given material using a training dataset that human scientists have labeled with the “right” answers. Once it’s trained and passes accuracy testing, the AI can then go on to predict the properties of new materials. Engineers can then use these predictions to identify more materials with new properties that would fit a particular device they want to design.
Before the NCCU team could develop that kind of AI, though, they’d need a training dataset. The amount of such information already available just wasn’t enough for the job. So the classroom project would focus on using molecular dynamics (MD) and first-principles calculations to explore the properties of simulated molecules and obtain their detailed mechanical and chemical behaviors.
The kind of data that such MD simulations would generate would be vast, they realized. In particular, exploring the behavior of tens of thousands of atoms — necessary for the material to act as it would at the size of real-world devices — would require a computer with a huge amount of memory and computational capacity. PSC’s Bridges-2 advanced research computer was the perfect fit for the project.
The massive computing power needed to generate a complete dataset is due to the two-fold parameter chirality that characterizes the carbon nanotube. Depending on the chirality, the properties change drastically, and this is what the students are investigating — changing the chirality and studying the mechanical properties under tensile loads.”—Fozia Sahtout Karoui, NCCU
The students began their studies with simulated tensile tests on carbon nanotubes. These chemicals are a kind of atomic-scale tube built from a lattice of carbon atoms. Scientists can “dope” carbon nanotubes with other atoms to change their electrical and chemical behavior. An important phenomenon the students captured was caused by the CNT’s chirality — when a material’s atomic structure is not identical to its mirror image. The behavior of mirror-image-but-not-identical molecules can differ in unexpected and useful ways.
In their tests, the students simulated what happens to the atoms in the material as nanotubes are stretched to and past their breaking point. Materials stretch and break in stages. First, they deform elastically — they stretch without otherwise deforming. Then they deform plastically — as they stretch they deform, thinning (“necking”) as the stress builds up near what will be the fracture point. As they ran each molecule and its chiral forms through to breakage, they collected the resulting data in a database, for a future ML AI to train on.
Importantly, the students didn’t just collect simulated data — as they simulated, they compared the results to real-world laboratory findings. That way, they made sure their simulations were making accurate predictions. They wrote up their findings on an initial set of about 800 nanotubes with different chirality for a presentation and short paper at the U.S. Department of Energy’s Graduate and Undergraduate Research Symposium. Their presentation, “Carbon Nanotube Mechanical Properties Using Molecular Dynamics and Development of Database for Machine Learning,” won the symposium’s first-place award.
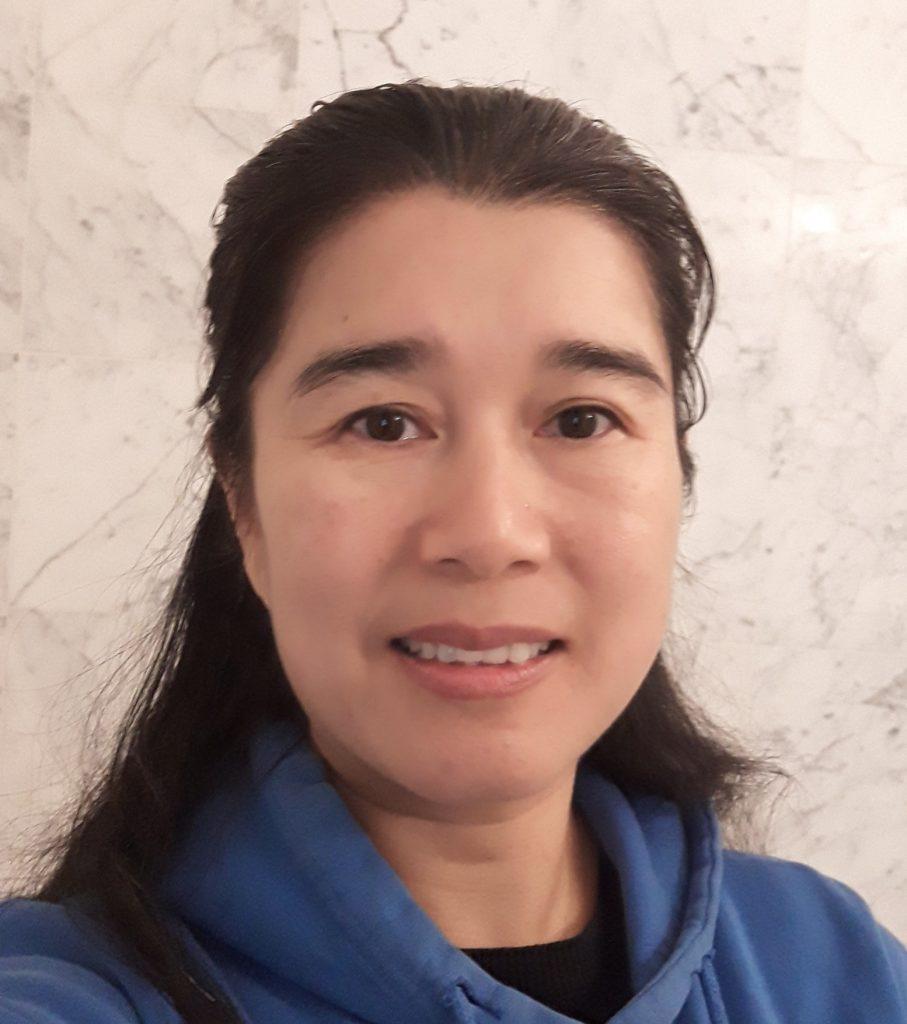
We have some deep learning training data for the carbon nanotubes working now. I think we have some new data based on ML calculations on about 800 CNT with various chiralities. Now it is time … to retrain the model. The accuracy is pretty good [so far].”—Gaolin Zheng, NCCU
The NCCU team continues to work, both with students and in their own research, on improving and expanding the database. Their initial ML use of the growing database has generated promising results. Now that the students have begun simulating the elastic behavior of the materials, the next steps will be to engineer CNT-based materials (such as CNT bundles, CNT ropes and so forth) and modeling how the electrical behavior of the materials changes with deformation. They are currently preparing a journal paper describing the students’ initial work.